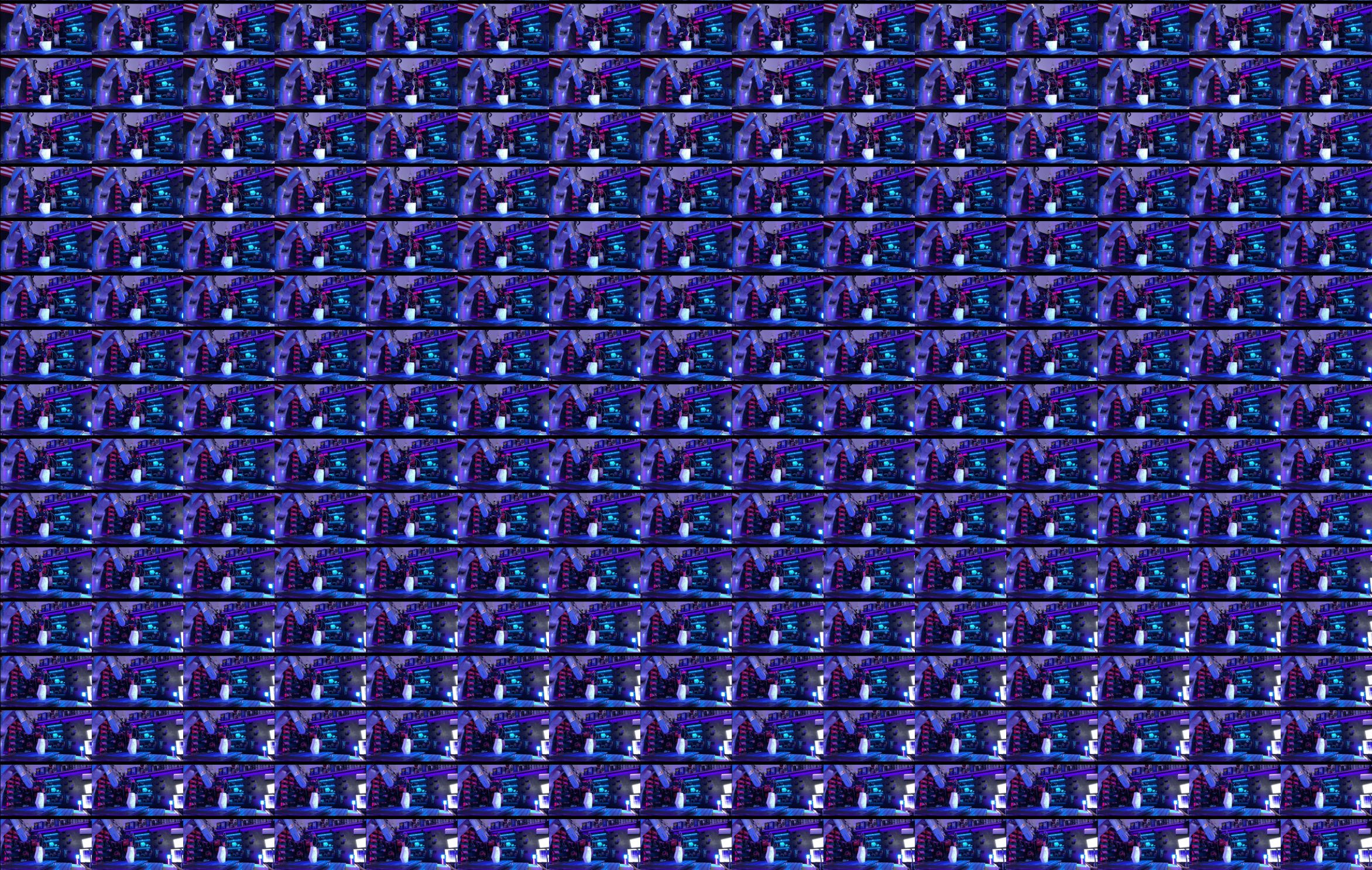
Multi-Axis Robotic Architectural Detailing
A process of 3D Scanning, Generative Design, and Robotic Fabrication
In collaboration with Austen DeGrenier
The construction industry is an inherently complex system with many factors such as environmental, material, and design. As architectural design has transitioned to utilizing digital tools for design methods, the construction industry has required more custom solutions for fabrication. With designs becoming more complex, the ability to meet design tolerances has decreased. Utilizing robotic solutions for manufacturing will allow building construction to meet the tolerance needs and provide more efficient buildings. Additionally, new material processes and handing techniques may bridge the gap between complex form and fabrication.
This project focuses on construction techniques located at the scale of the detail. I am currently interested in the application of Multi-Axis 3d printing and how Lidar 3d scanning can assist in Generative Digital Design. During the design and construction process tolerances, issues can become apparent and adjustments will need to be taken in consideration. Using Lidar 3d scanning we are able to scan and digitally create dimensionally accurate point cloud models; these models then can be placed in Computer-Aided Design (CAD) software and used as a reference in comparison to what was digitally modeled. When the tolerance deviation has been accounted for, we then can use an algorithm in CAD to generate an optimized joint based on user-defined constraints.
This project features a Denso Vs-087 Industrial 6 axis robotic arm. A custom designed extruder was required for this project as there is no off the shelf products. The extruder itself is a combination of a Bondtech QR 3.0mm gear drive extruder and an E3D Super volcano Hotend with a 2.0mm nozzle diameter. Additionally, a custom Extruder control box was required. I used a PID temperature controller for the hot end and an Arduino and stepper drivers to control the extruder motor.
The Procedure:
I am using methods of mobile 3d scanning from an Apple Ipad Pro’s Lidar sensor. Using an app called Site scape I am able to accurately capture data from the physical world, prepare the point cloud scan, and embed it into Computer-Aided Design (CAD) programs such as Rhino3D. I then take the reference geometry and I am able to create digital representations of the work environment. Lastly, I am using a Rhino3D/Grasshopper Script to generatively design connections between members in space and create a join that is optimized for Additive Manufacturing. Shown below is a stop-motion video showing the process and the final result overlayed with the 3d scan.
After the Generative design scripts from Rhino/Grasshopper produce the joint I move the CAD model into RoboDk. RoboDK is a low cost robot programing software with integrated CAD plugins for Rhino 3d. I am easily able to program, simulate, and run my designs with this software.
Once the program seems fit for production , the file is sent to the Denso Vs-087 and the part is manufactured. The video below is a time-lapse of a test print. The images following is the assembly and final production of a joint that could be found in a facade element in architecture.